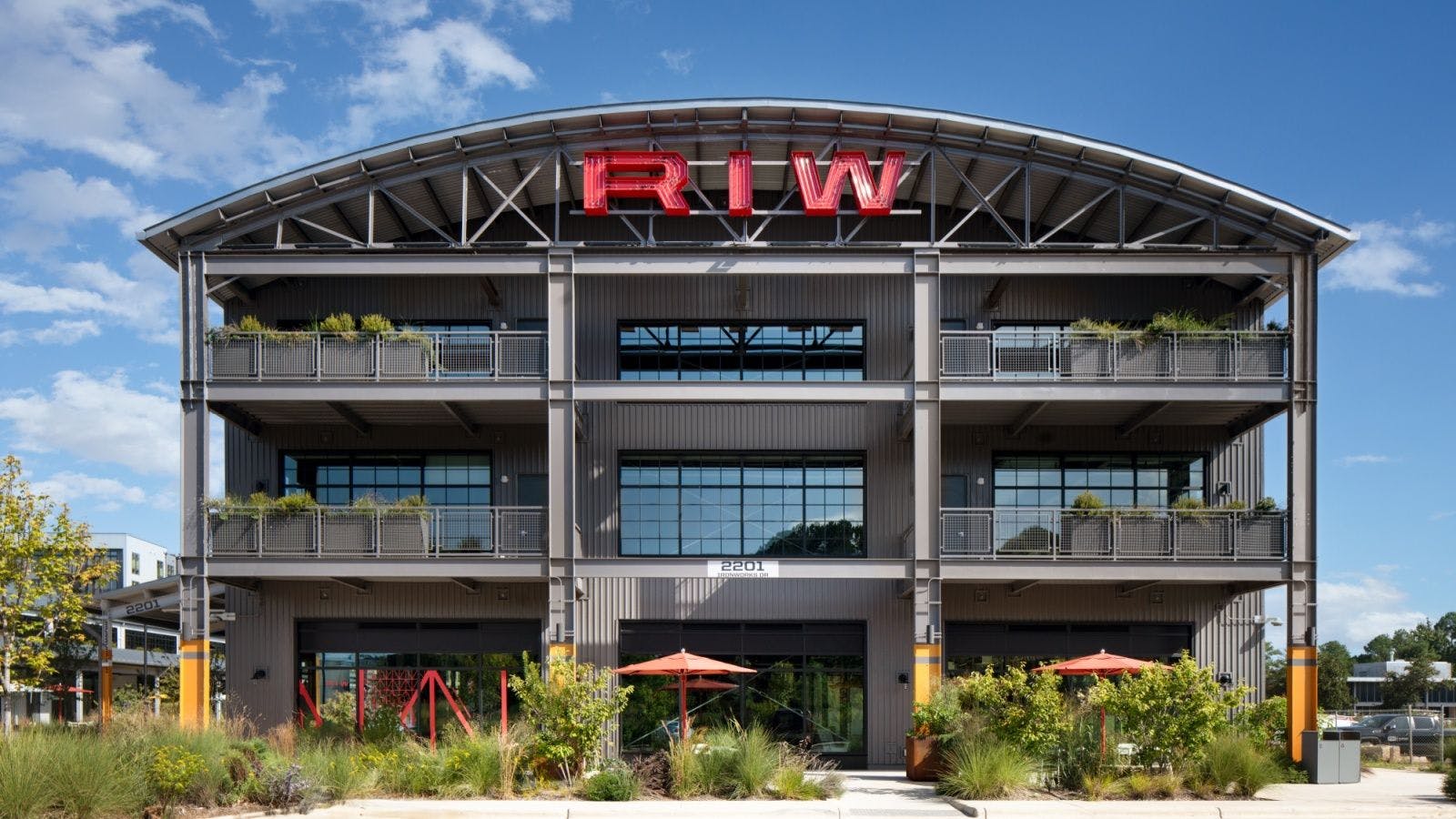
Plan of Steel: Raleigh's Newest Adaptive-Reuse Project
A former steel fabrication and manufacturing plant might not be the most obvious candidate for an adaptive-reuse project. But Grubb Ventures, which purchased the Peden Steel facility in Raleigh, North Carolina, in 2017 following its previous redevelopment of Dock 1053 just across the street, saw the site’s potential to become a vibrant mixed-use development—and found the ideal partners in co-owner Jamestown and general contractor Brasfield & Gorrie.
James Peden purchased the plant, then known as Raleigh Iron Works, in 1931; in the 1950s, he added the Bow Truss building, which was built in downtown Raleigh in the 1800s and where munitions were manufactured during World War I. Peden relocated Bow Truss to the iron works, which he renamed the Peden Steel Company and grew into the prime steel manufacturer in the state until its dissolution in 1984. Following that, the site was employed for odd jobs—like a skate park and, most recently, a waste-management facility that closed in the early 2010s. Falling into disuse, the property sat silent yet formidable, its interior growing dusty, dingy and decrepit, but its steel frame waiting to be repurposed.
Grubb and Jamestown first invited Brasfield & Gorrie, which is headquartered in Birmingham, Alabama, to walk the abandoned site not long after they bought it, in early 2017. Hunter Nichols, a Brasfield & Gorrie senior preconstruction manager and the project’s lead estimator and project manager who was part of that visit, says his company “quickly shared Grubb’s vision.”
In fact, everyone was so in sync that the traditional bid process went out the window. “We engaged Brasfield on a design-assist approach early in the conceptual planning of the process,” says Anthony Smithson, managing director of development for Grubb, “so we never went through a true competitive RFP process.”
A VISION FOR THE FUTURE
The shared vision for the project—(re)named Raleigh Iron Works—flourished following that initial walkthrough in 2017. Brasfield & Gorrie was officially awarded the final contract on Jan. 26, 2021, and began construction on Feb. 1. The scope of the project was large—an initial budget of $41.4 million, a 199,000-square-foot campus, two separate buildings, LEED design elements, potential biohazards and a stringent timeline of just over one year—and the company’s experience with similar projects was a crucial selling point. “The adaptive-reuse concept is something we’re really familiar with,” says Dana Green, regional marketing manager for Brasfield & Gorrie’s Carolinas team, “as well as maintaining the integrity of the spaces that used to be there, what they promoted and stood for.”
Among Brasfield & Gorrie’s portfolio is the recently renovated 95-acre Park Point campus in Durham, North Carolina, which like Raleigh Iron Works involved an existing warehouse and required a quick build-out—in this case, six months—for a life-science tenant. Brasfield & Gorrie turned Park Point’s four core shell buildings into creative office and science and technology space, complete with 30,000 square feet of both indoor and outdoor amenities. The project earned the company multiple awards, including an ABC Carolinas Excellence in Construction Eagle Award.
For Raleigh Iron Works, Grubb and Jamestown brought in S9 Architecture, based in New York City, as the lead designer and original architect to develop the plans; LS3P was the local architect of record, charged with executing the project on the ground alongside Brasfield & Gorrie. Brasfield & Gorrie also employed several subcontractors throughout the duration of the project.
It was a complicated redevelopment, starting with 71,000 square feet of restaurant, retail and fitness facilities, 170,000 square feet of creative office space and 219 residential units. Then there were the amenities and flourishes, such as a pedestrian promenade dubbed Peden Way, a plaza outside the multifamily complex called The Yard, a historical trellis structure known as The Stacks (previously used to literally stack steel delivered to the plant), a courtyard and multiple outdoor terraces in each building, indoor and outdoor seating at top-rated dining establishments, an indoor fitness space, outdoor spaces dedicated to community-centered placemaking, hands-free common-area doors and upgraded HVAC. And all of it in perfect proximity to downtown Raleigh, which sits just three miles south.
SLIDING INTO HISTORY
While sharing the creative vision of the project’s owners and having just completed an adaptive reuse of similar size, budget and timeline, Brasfield & Gorrie had additional considerations when redeveloping the Peden Steel property.
First, the campus was split across nineteen acres and two separate buildings, both original to the property in structure and name—Double Gable, which took $24.5 million of the original budget, and Bow Truss, which took $16 million. With the buildings being longtime fixtures of Raleigh’s industrial landscape, did the contractor run into any historical ordinances that restricted its redevelopment plans? Surprisingly, no. The property had been sitting dormant for nearly a decade before Grubb and Jamestown bought it, and everyone—from the developers to the city to residents—wanted to see it brought back to life.
“The client really wanted to repurpose the historic building and invigorate its integrity of being a fabrication mill and warehouse,” Green says. “They wanted to maintain its historic look while giving it a fun new energetic space that drew people in. So, they designed some really beautiful features with exposed beams and natural lighting, but also gave creativity to its office space and retail and access to green and outdoor spaces. Plus, the adult size slide is a huge hit.”
Yes, that’s right: an adult-size slide. It’s exactly what it sounds like—a fun and functional way for residents and visitors to transport themselves from upstairs in the Double Gable building down to the main plaza, or perhaps back in time to their childhood. “They just really wanted to make it a fun and lively space,” Green says. (See “The Fun Is Just Getting Started,” p. 41.)
GETTING THE LEAD OUT
The design included elements that would award the Double Gable building LEED-ND v4 Gold status, but transforming what was once an industrial steel mill into an environmentally friendly community for families would take some tinkering. Fortunately, Brasfield & Gorrie always plans—and budgets—for unforeseen elements and circumstances, which on this project included lead in the ground soil, as well as structural instability and some lagging effects from the COVID-19 pandemic.
The team employed ground-penetrating radar to detect what was underneath each building prior to beginning demolition work, which revealed necessary structural bracing repairs, a railroad track cast in concrete under the foundation as well as a differential of 18 inches between the original as-built drawings and the actual position of the building. They also worked with Mid-Atlantic Associates during a soil-testing process, which revealed lead-contaminated soil.
The lead came from the paint on the steel in the original Peden Steel building; when workers in the building washed their equipment, it would cause the lead to seep into the ground soil. When Brasfield & Gorrie’s crews discovered this contamination, “They had to halt everything and make sure that they had the expertise to come in there and extract the hazardous materials,” Green says. “They used HEPA filtration vacuum cleaners, so the dust wouldn’t go everywhere, and then exhaust ventilation to collect it so as not to affect the surrounding air quality. Everyone stayed safe, and the team ensured they were building in a safe environment.”
Once the lead was removed, the next step was to fortify the buildings’ existing structural steel with temporary bracing while certain structural elements were demolished. New steel was also installed to sustain the weight of the added floors and amenities. Brasfield & Gorrie brought in a structural engineer, who helped design a frame that would provide appropriate strength and safety. The team was even able to use hundreds of 6-feet-by-2-feet bin blocks they found onsite as anchors for the temporary bracing, so no time or money was wasted.
Then it was on to removing the concrete-encased railroad tracks and mitigating the foundational discrepancy—unforeseen and not at all common issues, but nothing Brasfield & Gorrie couldn’t handle. “Of course,” Green says, “on an adaptive-reuse project, there are unforeseen existing conditions which aren’t necessarily shown even through great technology.”
PRESERVE AND PROTECT
Other conditions, such as those posed by the pandemic, were foreseen and prepared for ahead of time. Supply-chain issues and long lead times were among the biggest challenges resulting from COVID, which was still a disruptive force when the project broke ground in early 2021. “We combated that by ordering all of the materials immediately, and stored them in the empty warehouse onsite,” Nichols says. “The warehouse was originally supposed to be demolished at the start of the project, but we suggested keeping it intact, so that it could be utilized for storage. It worked out perfectly.”
That was part of “the beauty of developing a project in the middle of an old steel fabrication site,” Smithson says. “We had empty warehouses available to store material. Brasfield & Gorrie identified issues with the supply chain early in the project, and we were fortunate to be able to procure all long-lead-time items and store them in a warehouse that was 50 feet away from the project site.”
But some of the project’s materials didn’t have to be ordered at all—because they were already there. Between 85 and 90% of the original steel remains within the two buildings. Smithson says: “We also saved many of the relics from the demo process—the original bridge cranes, trellised strut braces, bar joists and steel girders—to be used in art installations, swings and other features throughout the site.”
Visitors can see the original steel intertwined with the new design throughout both buildings. Two of Nichols’ favorite examples are the courtyard central to the Double Gable building and the exposed roof framing in Bow Truss. “New structural steel framing was added only as needed to support the additional elevated slabs,” Nichols says. “The design teams were careful to utilize and feature as much of that [original] steel as possible.”
LEED BY EXAMPLE
Another design element that was no less complicated than mitigating unforeseen circumstances was the pursuit of LEED certification. It was important to the project’s owners that the formerly industrial facility embody a commitment to the integration of green infrastructure, public transportation, pedestrian-friendly community design and overall innovation. Raleigh Iron Works’ LEED features include bicycle facilities and accessibility to alternative transportation; outdoor spaces featuring native plants to help manage stormwater runoff and heat-island effect; high-efficiency water fixtures; indoor air-quality assessments; and new materials evaluated based on their lifecycle and environmental impact.
In addition to designing for the wellbeing of the environment, the team designed for the wellbeing of the user, incorporating elements of thermal comfort, natural light, amenable acoustics, outdoor views and, of course, ADA compliance throughout. They also plan to pursue additional building-level certifications such as LEED Core and Shell.
RALEIGH REVIVAL
With so many different uses for the new facility, it might seem hard to pick a favorite. That’s why Green says she loved “being able to see it come to life. I loved how the project team was able to transform it from something that just sat there and didn’t draw anyone in, into a place that people can’t stop talking about today. And that’s something I love—that sense of community and being proud of something I’ve been a part of with a team that has built something for the community.”
Nichols favored the more technical aspects of the project, but with no less pride. “For me personally,” he says, “being involved in the preconstruction process through several iterations of design, providing timely budget information to guide decisions, and then managing the actual construction until turnover was one of my greatest professional achievements. I’m proud to have helped bring Grubb’s vision to life.”
As Raleigh Iron Works—which recently received Eagle recognition in ABC’s 2024 National Excellence in Construction® Awards—is not only a testament to the future but also an homage to the past, Smithson says, “The decision to keep the steel in its original condition, the repurposed salvaged material throughout the site and the creative storytelling of the history through art retain this community’s connection to its former life as the Peden Steel fabrication facility.”
Related stories
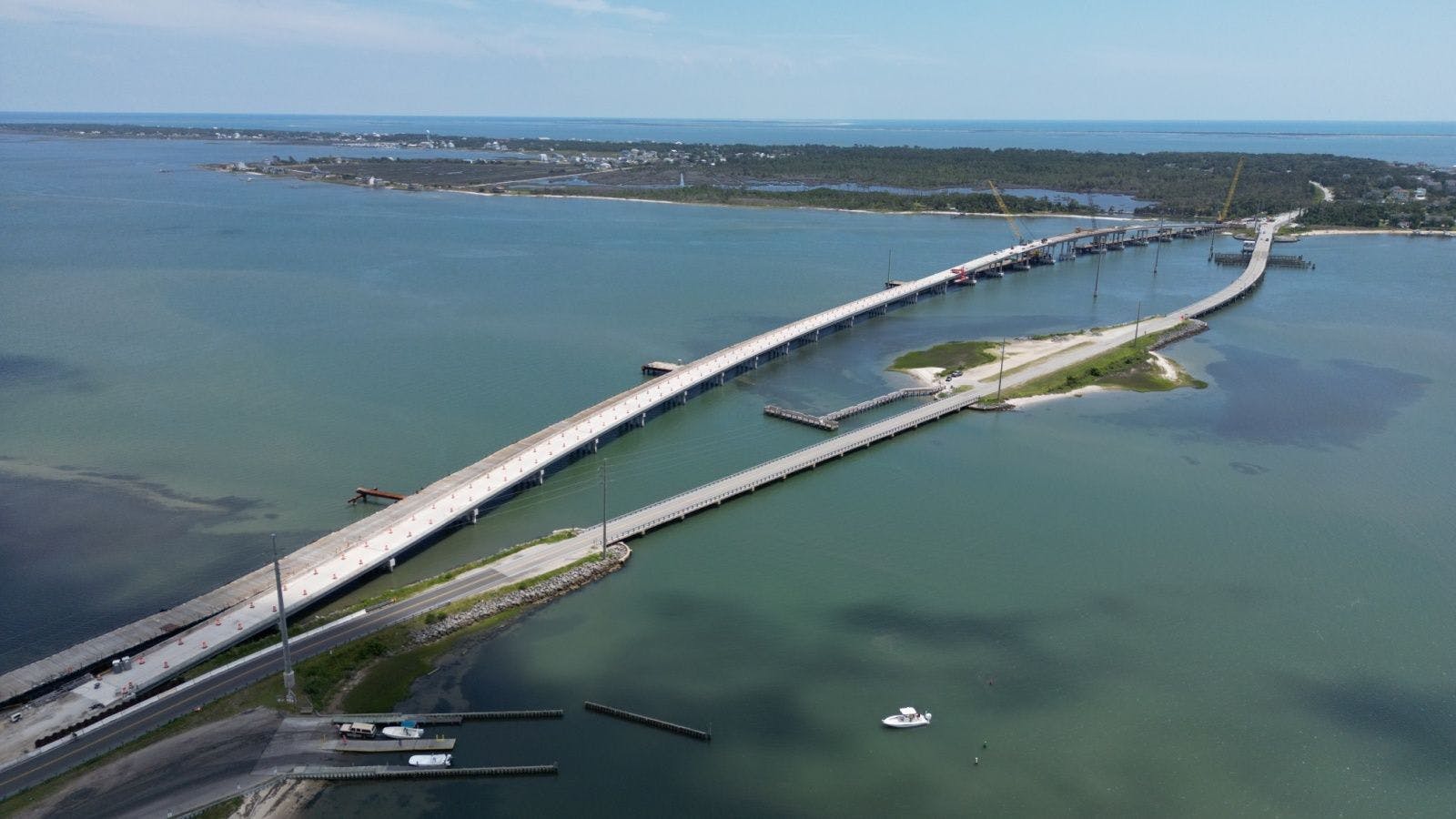
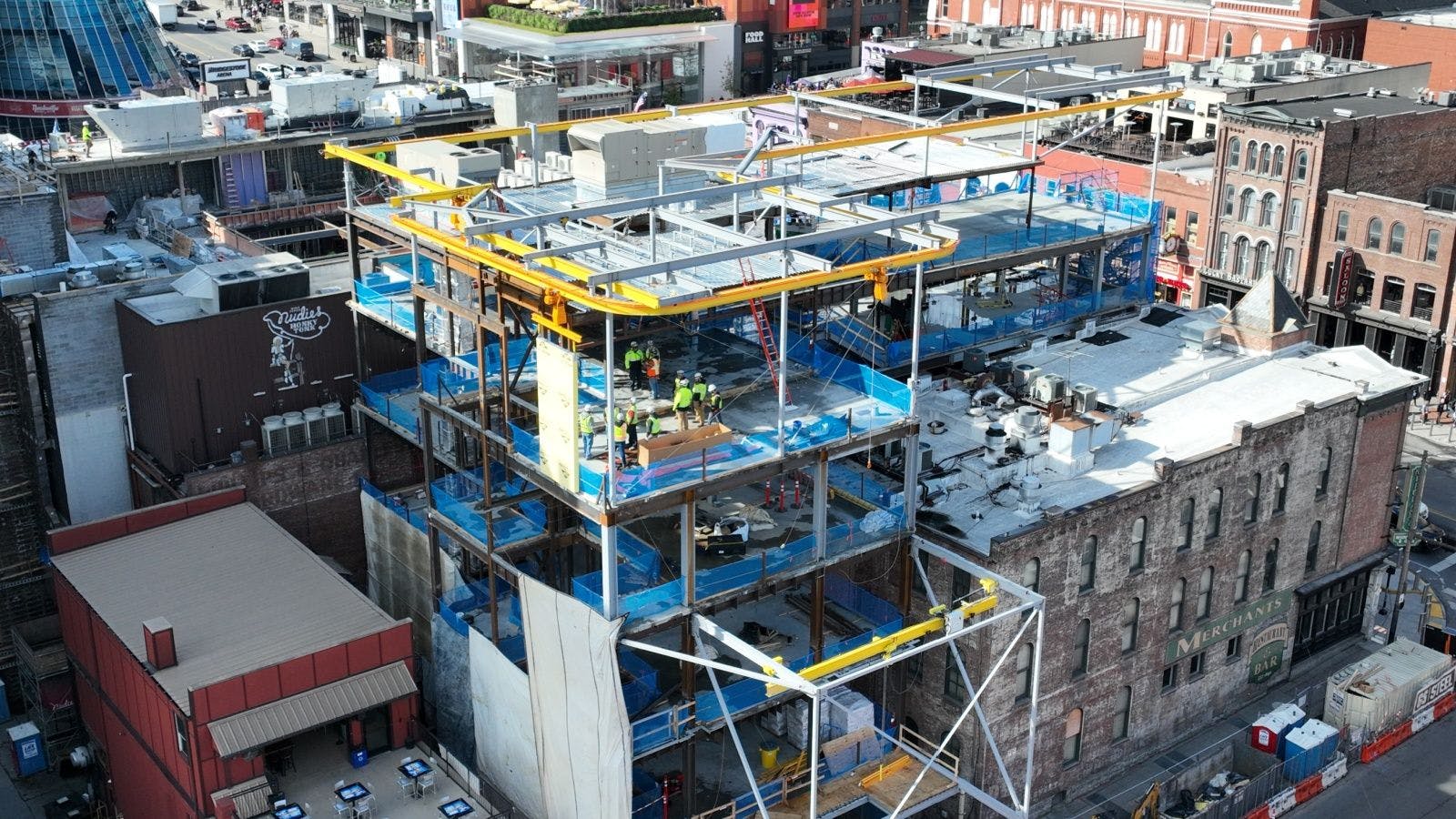
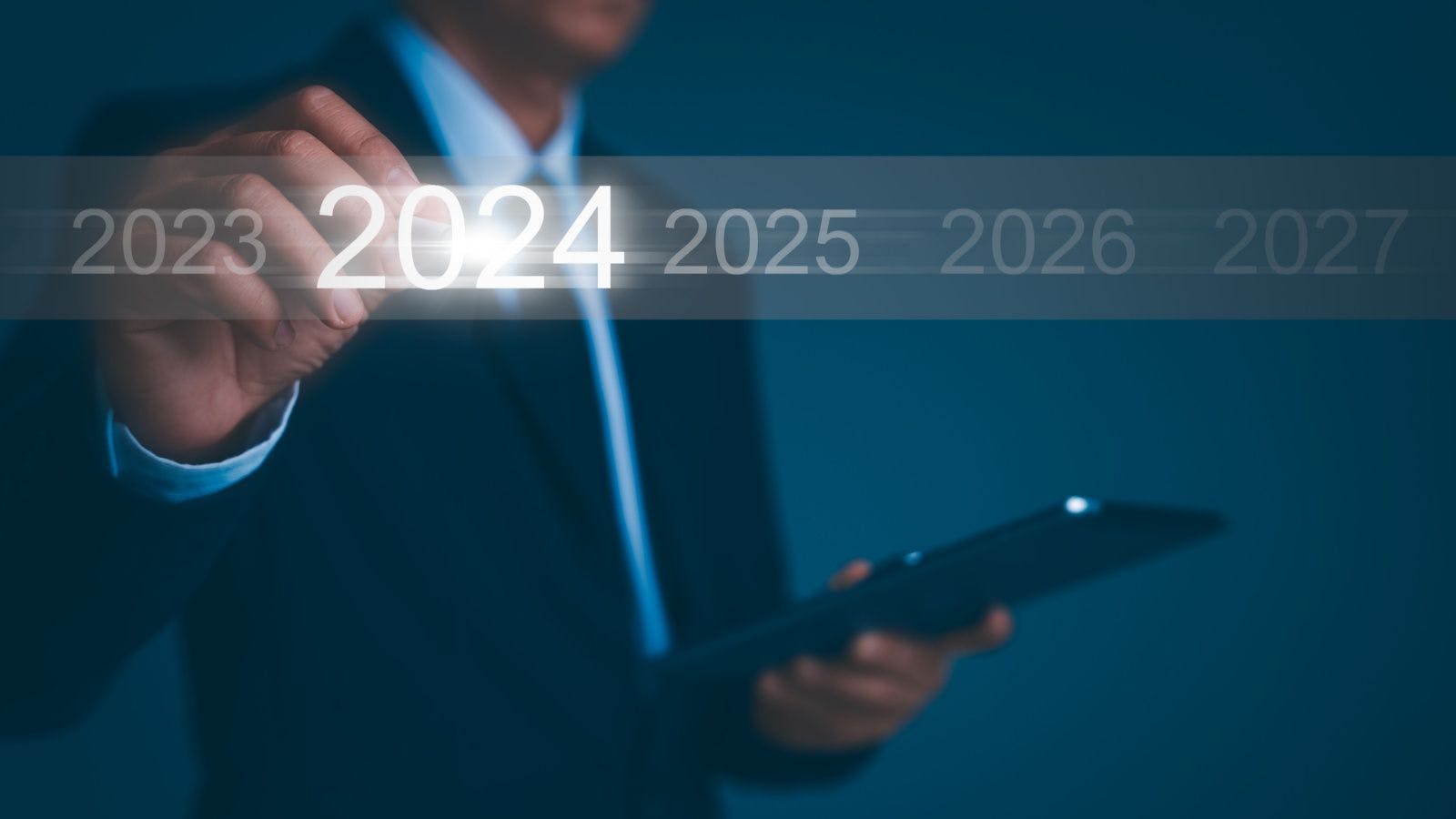