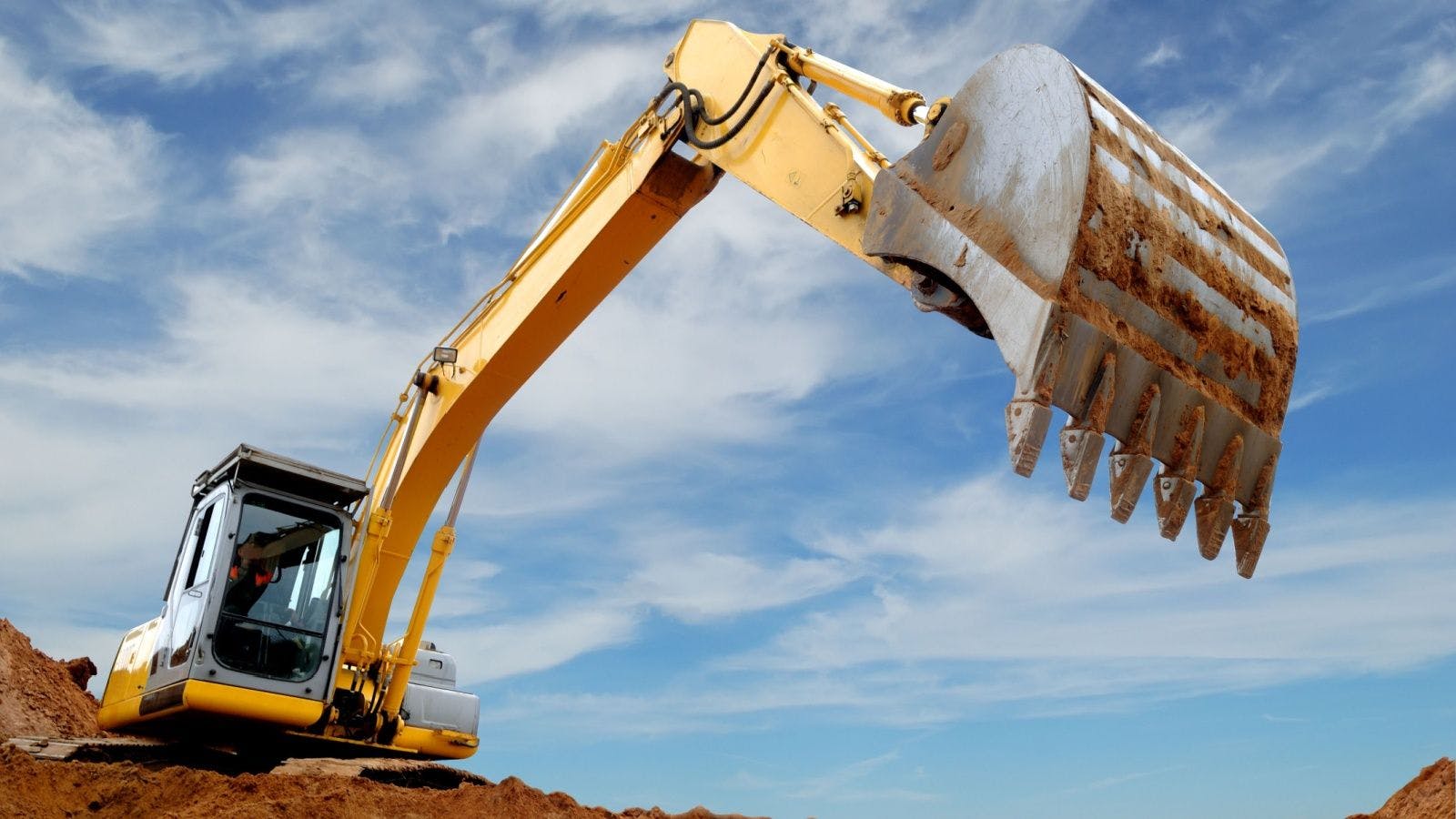
Mitigating Struck-By Incidents on the Jobsite
According to the Bureau of Labor Statistics, there are roughly 150,000 injuries each year on construction sites. Many of these injuries can be avoided through more effective planning, communication and training.
Struck-by incidents account for nearly 20% of all construction fatalities. These incidents include workers being backed over or run over by equipment or vehicles, pinned between equipment or other objects, struck by swinging equipment parts or falling loads, and crushed beneath overturned equipment and vehicles. Yet, the measures taken most often by contractors to protect workers from these struck-by hazards are personal protective equipment, back-up alarms and use of spotters. These are passive measures and by themselves are not do not entirely eliminate incidents on their own—contractors must implement more proactive controls to complement these existing measures and prevent injuries and fatalities.
Most struck-by fatalities on a construction site involve heavy equipment and trucks. This is why it is crucial to understand the challenges this equipment presents while operating and for those working in proximity to them.
PLAN IT OUT
The first step in addressing these hazards is to develop a site plan for establishing worker, equipment and vehicle travel paths to minimize conflicts and reduce the need to travel in reverse. Contractors should consider all possible conflicts between workers and equipment onsite such as parking areas, vehicle entrances, toilets, material laydown areas, stockpiles, etc. This site plan must clearly define and identify work sequences, locations and movements of equipment and workers, and how these conflicts in travel paths are resolved. Contractors must ensure this plan is communicated to each worker and is updated as site conditions change.
One of the major reasons for struck-by incidents are line-of-sight issues created by equipment size and design. Blind spots are areas around equipment that are not visible to the operator, either by direct line-of-sight or indirectly by use of internal and external mirrors. These blind spots can vary with each make and model and are also affected by attachments being used and loads being carried. Larger equipment has larger blind spots.
Equipment operators have an appreciation for this, but workers on the ground often do not recognize the specific locations of equipment blind spots. Each worker should know where the safe zones and no-go zones are for each piece of equipment onsite. New technologies are being introduced to manage this risk, such as cameras and proximity sensors. However, these technologies have challenges and limitations due to mounting positions, operating environment and detection sensitivity.
TRAIN, TRAIN, TRAIN
It should be noted that while these technologies are useful, they do not replace the need for worker training. Greater communication is required between equipment operators and workers on the ground in identifying blind spots for each piece of equipment on site.
Workers on the ground should not only understand where blind spots exist but also the equipment swing paths and the importance of staying out from under overhead loads. Contractors should also establish safe procedures for approaching heavy equipment that is in use. The most important action is to make eye contact with the operator and signal your intent to approach them.
Many accidents have happened because an equipment operator was unaware that a worker was behind them or beside them. Equipment operators should also make it safe for workers to approach by positioning the equipment so workers can safely climb steps or ladders to access the cab, lowering any attachments and placing the machine in neutral/park and setting the brake.
SOUND IT OUT
Communication between workers is also affected by noise levels and distance from one another. In these situations, hand signals are often used to communicate. Workers should use standard hand signals as each signal is designed to be clear and distinctly different from other signals to avoid confusion. Where an operator’s view is obstructed, workers may utilize two-way radios. Procedures should also be established for effective communication as it relates to equipment function, direction, speed, distance and what to do when communication is lost or unclear.
Equipment and vehicle spotters should be required when backing vehicles with obstructed rear view and no back-up alarm, operating equipment in congested areas, or in areas with poor visibility. Operators, drivers and spotters must be aware of their responsibilities when backing equipment to avoid incidents. They should inspect the travel area for obstructions and other obstacles, agree on hand signals and discuss the vehicle movement plan.
It is critical that spotters have no other duties and remain visible to the operator while backing. Drivers or operators should stop the vehicle immediately upon losing sight of the spotter or if the spotter’s signals are unclear.
Worker and operator distractions may also contribute to struck-by incidents on a construction site. Rules should be developed to minimize distractions that lead to better recognition and improved communication. Common distractions include or involve wearing earbuds, headphones or other types of headsets that interfere with the user’s ability to hear warnings or other sounds that may alert them to danger.
Operators should be prohibited from wearing earbuds, headphones or headsets while operating equipment unless specifically used for signal communications. The use of cellphones by other workers should be limited to designated areas where hazards are well controlled.
As we’ve discussed, the frequency of struck-by injuries and fatalities involving construction equipment have been consistent for many years. Traditional controls involving personal protective equipment, back-up alarms and spotters have not been 100% effective at reducing this trend completely. Therefore, it is important that contractors establish methods for minimizing conflicts between worker and equipment travel paths by establishing site travel plans, increasing awareness of equipment blind spots, improving communications, minimizing distractions and establishing safety procedures.
Related stories
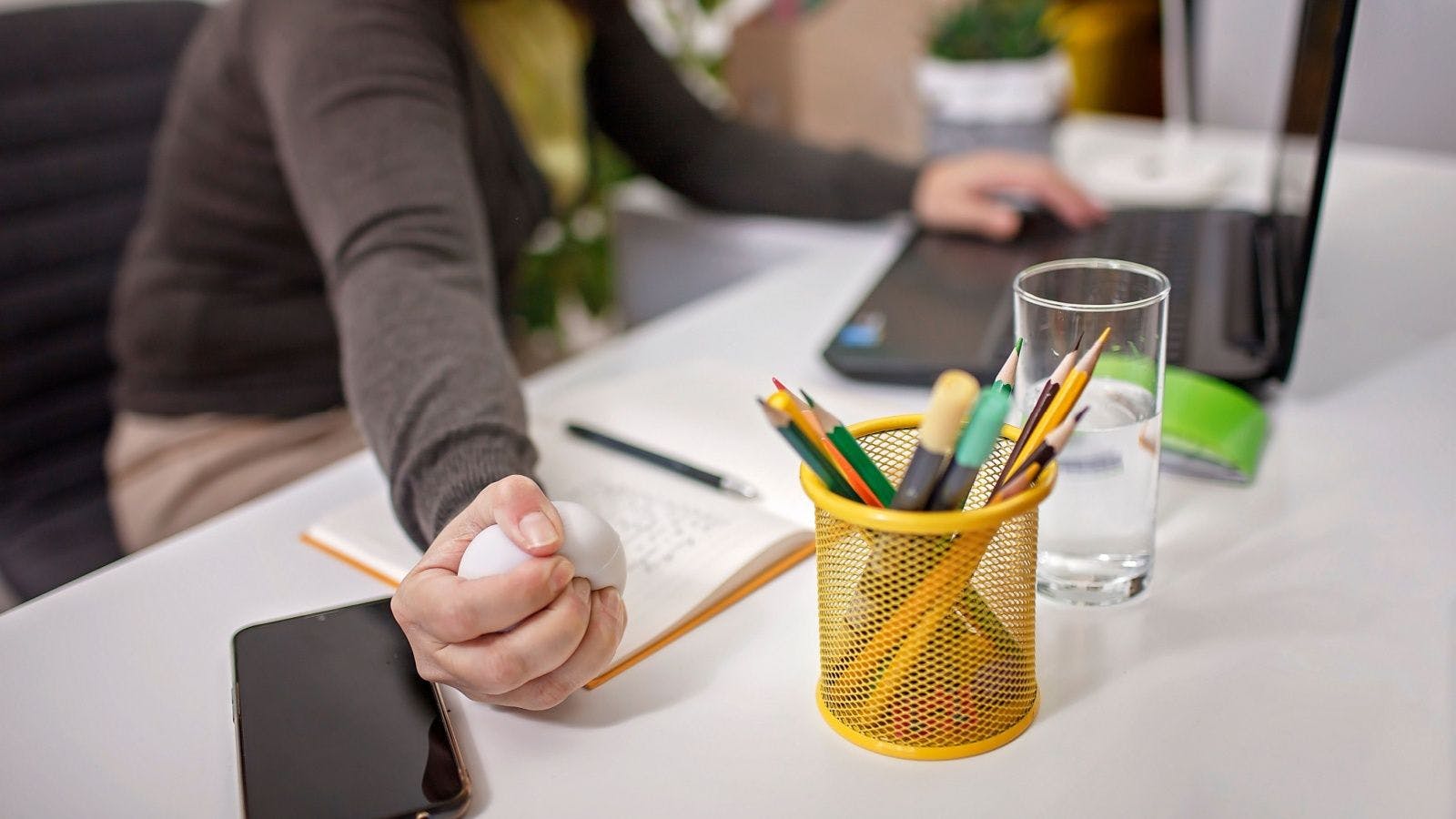
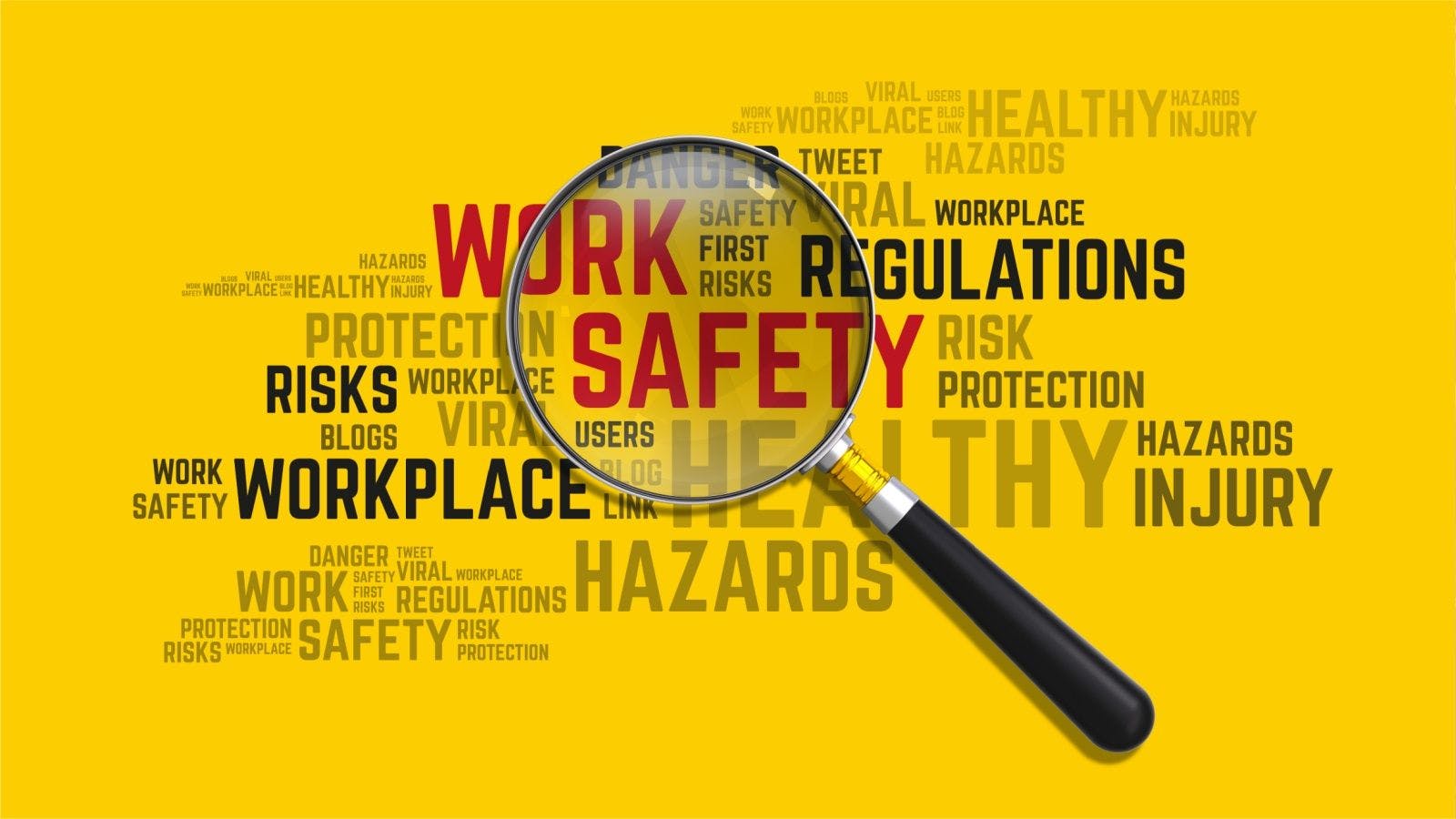
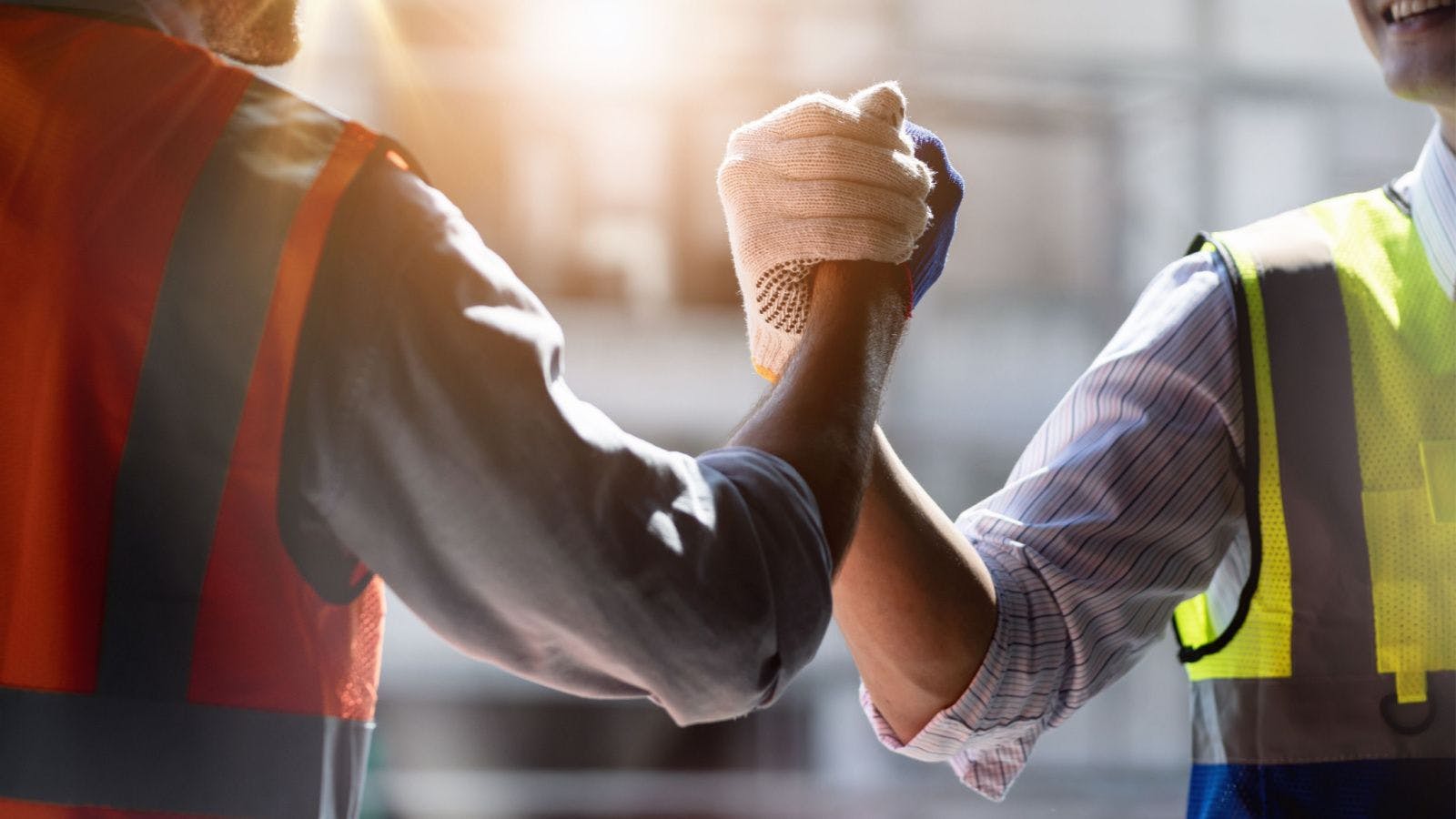