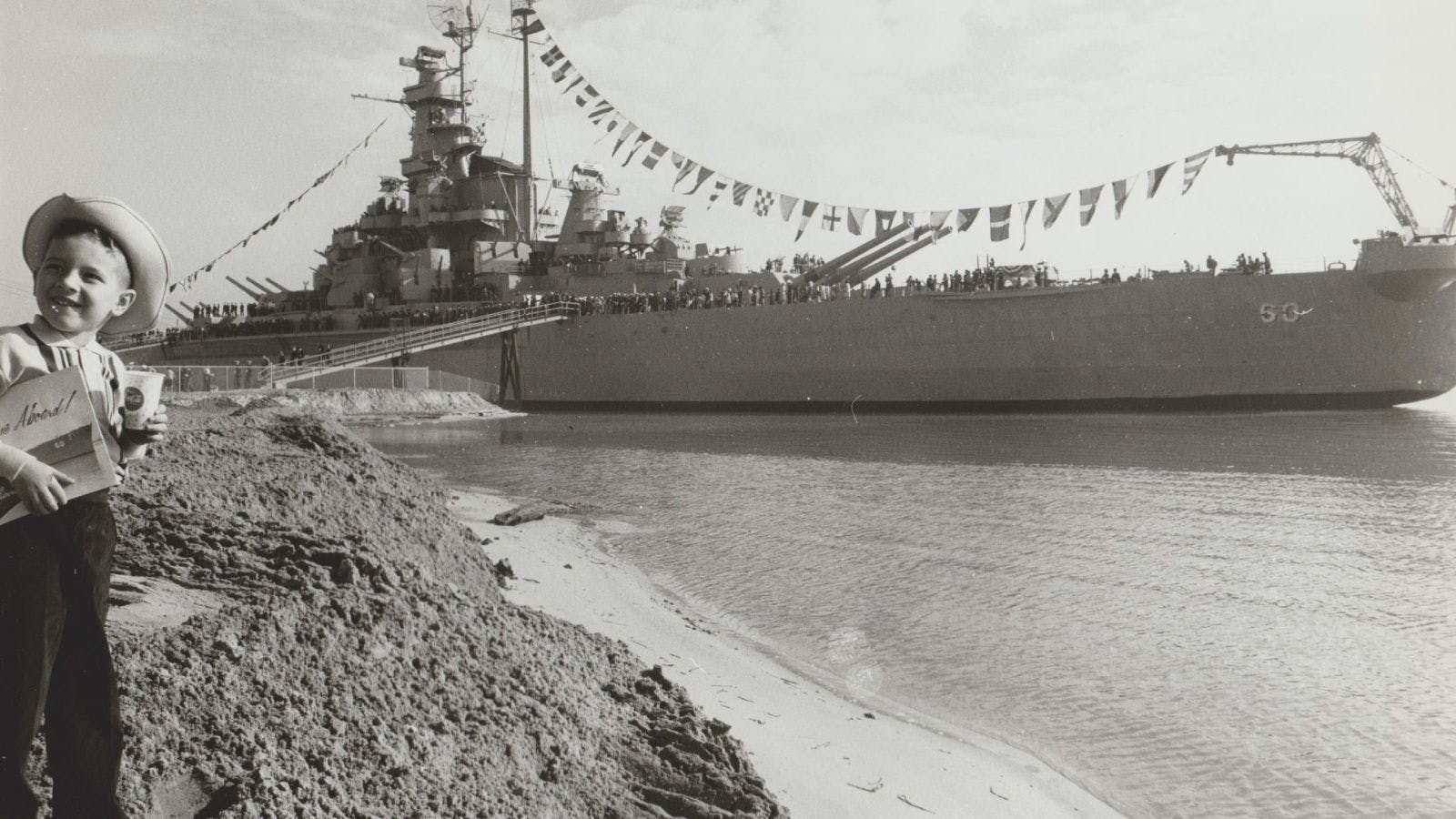
History on Deck: A Deeper Dive on the Restoration of the USS Alabama
On Jan. 9, 1965, the USS Alabama Battleship Memorial Park in Mobile Bay, Alabama, officially opened to the public. With 12 decks to explore, and resting alongside an aircraft pavilion, tanks and artillery, the submarine USS Drum and more, the Alabama has since garnered more than 17 million visitors and nearly $1 billion in state revenue over the course of its time in the public eye. But before it became a state attraction, the warship earned nine battle stars on active service during World War II.
Unsurprisingly, withstanding the events that earned the Alabama nine battle stars and a subsequent retirement in Mobile Bay eventually necessitated a restoration. But the restoration process for an award-winning WWII battleship, also unsurprisingly, is intricate and specialized. Most recently, Alabama’s original main deck was in need of serious attention thanks to years of war, sea air, sun and millions of museum visitors.
Following several small patchwork jobs over the years, the memorial park decided to restore the entire main deck in 2021. To complete the work while also maintaining full operational abilities of the museum itself, the park settled on a five-phase renovation to be completed over three years for $8.5 million.
And, thanks to the tempestuous weather around Mobile Bay and an unexpected kink in the supply chain, one of the most important components of the job turned out to be its surety bonding.
TECHY TEAK
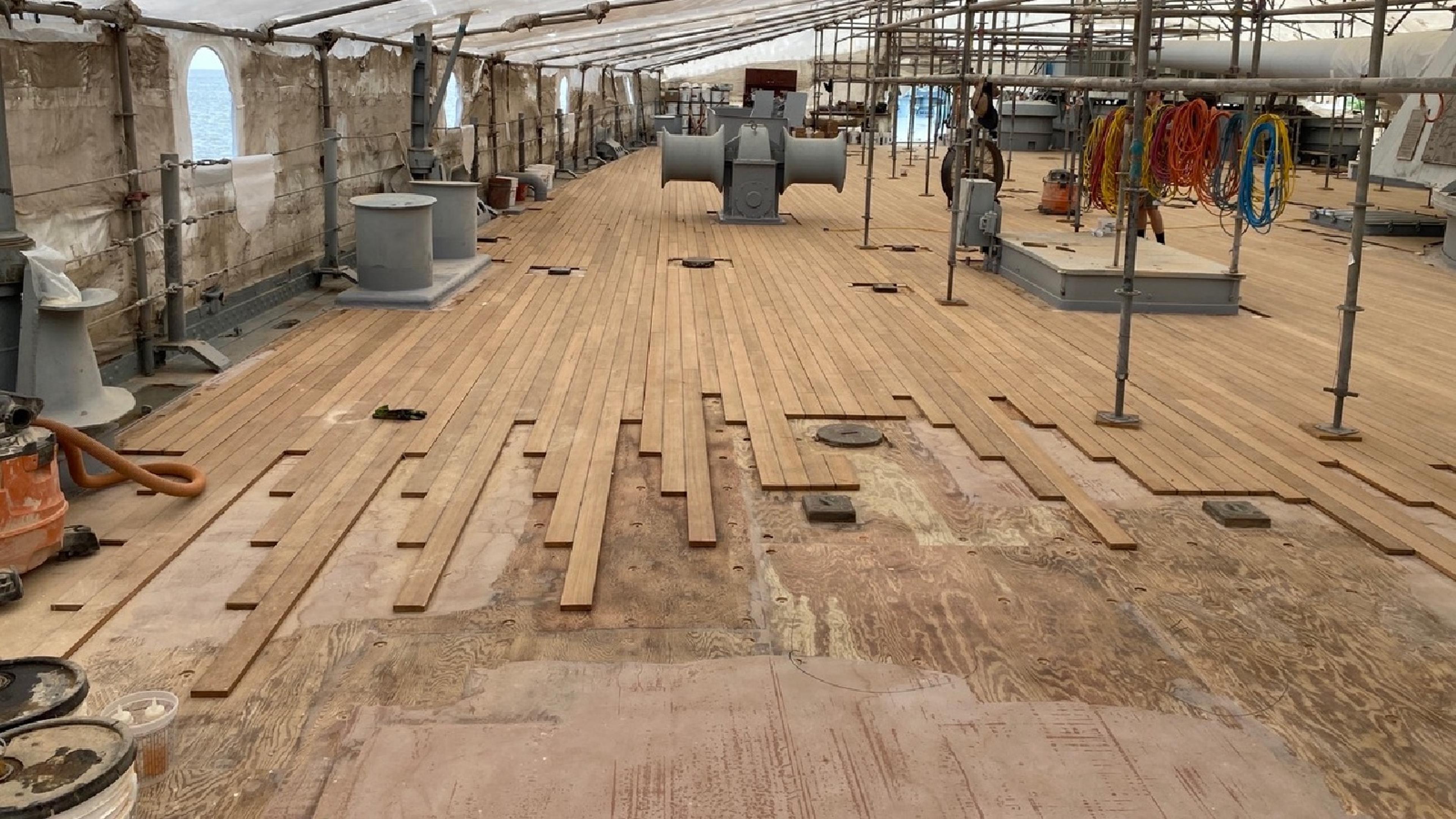
The project description mandated that the renovation completely replicate the Alabama’s original teak decking—and that the entire project be surety-bonded for the duration of the work. Youngblood Barrett Construction, based in Mobile, won the competitive bid process and was retained as general contractor, with Sarasota, Florida–based Teakdecking Systems as subcontractor for the teak work.
From October 2021 to October 2024, five areas of the main deck—totaling 20,752 square feet—would be removed and replaced according to exact historical specifications. The renovation of each area would include erecting a containment system for the removal and abatement of the original teak planks and any hazardous materials, dry blasting, priming, leveling and installing a plywood substrate on the steel deck, followed by the new teak panels, which then would be caulked and sanded.
Even a veteran battleship with a history as bejeweled as the Alabama’s is not immune to the turning tides of technology, so to help Youngblood Barrett complete each phase of the renovation to historical scale and accuracy, Teakdecking Systems applied its 21st-century approach. “As far as how the teak is installed, it’s probably a little different than how they did it 70, 80 years ago,” says Richard Strauss, Teakdecking’s CEO. “However, people value our specific installation process because they know that it’s going to last them a long, long time.”
Teakdecking’s process began with taking a digital scan of the Alabama. A Prodim Proliner machine situated on the deck of the ship digitally collected data points, similar to BIM. That data was then loaded onto a computer, from which Teakdecking created the primary drawings it would use to fabricate exact replicas of the ship’s original teak decking at its factory in Sarasota, about eight hours from Mobile. Teakdecking had to then deliver that decking to the Alabama in Mobile.
Scanning and high-tech techniques stepped aside for a tried-and-true truck haul. To prepare for the road trip, the teak panels for each section of the deck—each panel measuring roughly four feet wide and up to 22 feet long—were laid out on a manufacturing template at the factory and put together just as they would be on the ship. “All the trim is cut here, everything is prefabricated,” Strauss says, “so it looks exactly like it’s going to look when it’s on the ship.” He continues to explain the meticulous process of numbering and labeling every single deck element, “like a set of instructions for a piece of IKEA furniture,” but on a much grander scale.
Then came disassembly and packaging. Finally, each numbered section was loaded into containers with its respective set of instructions and shipped up and over to Mobile. Teakdecking team members went along to help direct this part of the process alongside Youngblood Barrett and other subcontractors. “Everything is really coordinated, all the way from the engineering to the build to the crating,” Strauss says. “So, when it arrives, they know what crate goes where on the boat and what orientation to face them.”
SURE THING
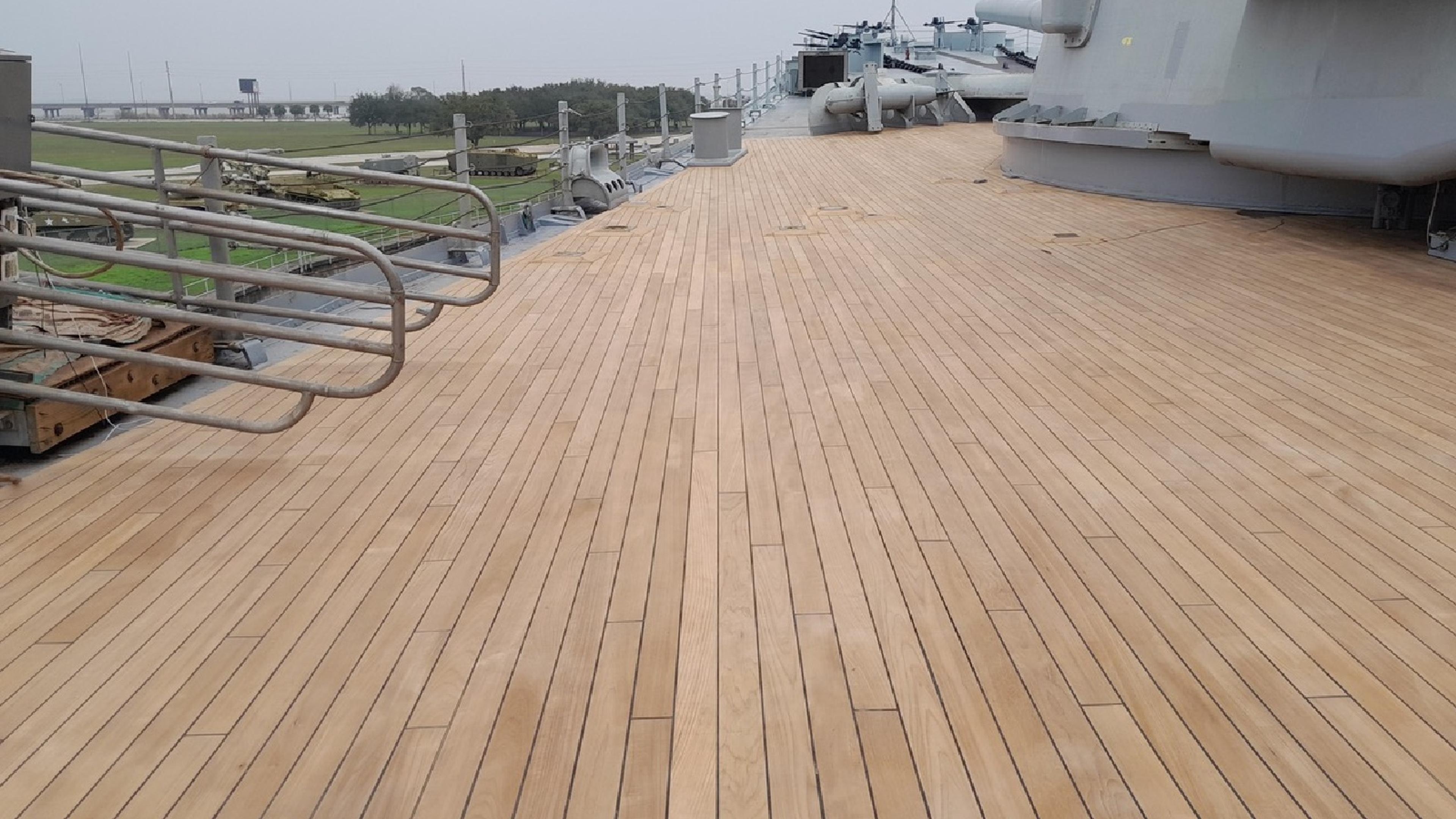
Using modern-day technology to rebuild history is a common occurrence for Strauss and his team, who have completed several similar projects prior to the Alabama deck restoration, including a current job on the battleship USS Missouri, which is now a memorial museum at Pearl Harbor. But the significance of this particular job wasn’t lost on Strauss or its other stakeholders.
In fact, the high-tech approach of the Alabama project is what excited Richard Sghiatti, regional vice president for Old Republic Surety, the surety bond underwriter for the job. “Of course, this isn’t just some yacht where there is plain, open decking,” Sghiatti says. “On Alabama, there are guns, pipes, cables or something else coming out from the floor all over the place when you walk through. So, there was a lot that had to be specifically engineered to fit properly. What I saw from Teakdecking and their approach was an outstanding job.”
Thanks to the cutting-edge technology, collaboration by all parties and their respective and collective expertise, the project was completed seven months ahead of schedule, in March. And good thing, too, since Alabama is berthed year-round in Mobile Bay, on the Gulf of Mexico, including through hurricane season.
Just as the Alabama once had to ride out a typhoon off the coast of Kyushu during its wartime service in June 1945, so too did it require protection from the elements during its restoration. During each phase of the project, the ship was covered and secured—so only select personnel were able to enter a specific area—to protect the ongoing work from the elements and any wandering visitors, as the museum remained open to the public during the duration of the project.
While that arrangement took a bit of finesse, it was where Youngblood Barrett’s and Teakdecking’s previous experience came in handy. And, while it was ORS’s first time bonding this type of project, the surety company’s specialty is adapting: listening to its contractor account, understanding the critical path of the job and what the strategy is to successfully complete the project. This was accomplished by having multiple meetings as everyone all came together to support Youngblood Barrett.
“We don’t specialize in [this type of project], but we adapt, because all construction projects are unique,” Sghiatti says. “There’s nothing cookie cutter about this or the other projects we’ve bonded. So, we look at that and we look at the expertise and financial posture of the contractor: how they’re going to plan it out and who they surround themselves with.
“In this particular case,” Sghiatti continues, “they had one of the best teak-decking contractors in the country—they’ve already done two other battleships. And all the critical-path subcontractors were bonded to Youngblood Barrett. Subcontract bonding was an important underwriting requirement for this project. If you start putting all the pieces together and you have the right players that have experience and knowledge, then it all comes together.”
MOBILE, WE HAVE A PROBLEM
Another instance of adaptation came in response to a less natural source: U.S. sanctions on Myanmar, the Southeast Asian country from which Teakdecking Systems traditionally imported almost all of its teak, imposed in response to the February 2021 military coup that deposed the democratically elected government. “In a ship of this magnitude,” Strauss says, “the size of the wood planks it would require [was substantial]. Myanmar was our traditional source of teak, but post-coup and sanctions, we’re sourcing our teak from plantations all over the world.
“And you just don’t have that old growth from these super-large trees anymore,” he says. “We’re dealing with smaller trees with smaller diameters, smaller heights. To source that much quality wood from a new plantation would just be … I don’t want to say virtually impossible, but impractical at least.”
Why not just source some other type of wood? What’s so special about teak? One, using a different wood wouldn’t be in keeping with maintaining the historical specifications of the project. Two, teak is an excellent wood for ships because of its ability to withstand harsh weather and provide a non-slip surface. While entire ships used to be built from teak, as it has gradually increased in cost and scarcity, it has remained the primary choice for trim and decking. This disruption to Teakdecking’s Myanmar supply chain severely altered the cost and availability of teak, as well as the project’s timeline—speeding it up.
Would this be cause to enact the surety bond? Sghiatti had logistical concerns but never any true doubts. “My biggest fear was getting the teak across from Myanmar all the way over to the U.S., because you had no idea what was in store for that ship,” he says. “Plus, it was still COVID. That was probably the biggest concern of mine when underwriting on the account. And, obviously, the project was new for us, but I had the confidence in our contractor and everybody involved with that organization that they would more than manage it.
“But this was definitely unique in the regard that it was a battleship and a museum we had to keep open,” Sghiatti says. “That was the other part that was pretty risky.”
Sghiatti and Strauss handled that risk through in-depth communication. “We did a lot of communication out front to let [Youngblood Barrett] know what our needs were,” Strauss says. “The logistics of the project were really put on the shoulders of the contractor, and they’ve been phenomenal. They’ve really done a great job for us and provided anything we’ve asked for.”
Teakdecking already had a substantial amount of Myanmar teak stored in its warehouses, and it was in the process of receiving more before the sanctions went into effect. They had just enough to finish the Alabama. But “going forward with some of these other battleships,” Strauss says, “we will have to be sourcing some other material from somewhere else.”
All of these issues, foreseeable and surprising, potential and probable, are why the USS Alabama Battleship Memorial Park required a surety bond in its contract. From hurricanes to sanctions, you never know what obstacles you’ll encounter on any project of any kind, let alone something as niche as a nine-star WWII battleship’s deck restoration.
PRIDE AND JOY
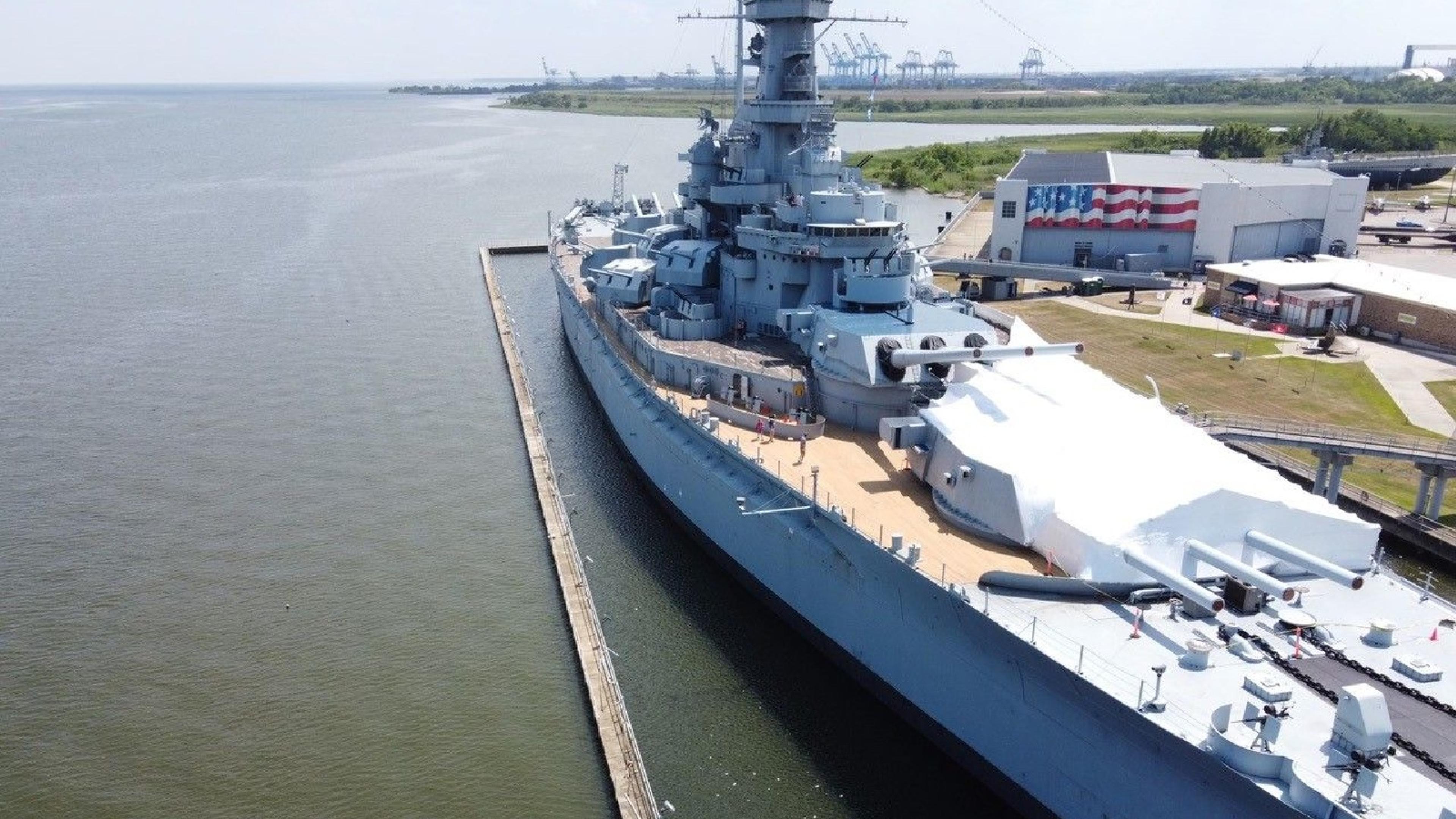
The modern technology, new teak decking and 21st-century challenges of this project don’t erase the historical significance of the USS Alabama, nor do they dampen the joy each stakeholder felt while restoring its deck. Similar to Sghiatti, the new technology was also part of what made this project one of Battleship Commission Chairman Terry Ankerson’s favorites since being appointed a commissioner in 1979.
“The digital scanning process that created an exact replica of the deck was amazing,” Ankerson says. “We saw photos of the deck sections being laid out on Teakdecking’s warehouse floor in Sarasota. Trucking the crates to Mobile, lifting them onto the Alabama—the logistics were well-planned.”
Strauss had more than one favorite thing about this project. “The first part is the amount of pride our employees take in the projects they do and when they see the end result,” he says. “It gives everyone such a good feeling. Our installation team has the hardest job in the world. They’re out in the heat, they’re out in the rain, they’re out in the cold, they’re out in the elements, and it’s not easy work, but they do it because the end result is phenomenal.
“And, of course, doing an iconic battleship is really cool,” Strauss says. “It is being part of the restoration of our history. We have a lot of people from the Navy [working] here, and they take a lot of pride in that, as they should. So, we always enjoy doing these projects. They mean a lot, because they are something the whole country can come and see and enjoy.”
Sghiatti is looking forward to being one of those people to visit the Alabama and enjoy it as a finished product. “I’m also looking forward to seeing Youngblood Barrett in their success,” he says. “We stepped up and provided the surety support, and they’ve proven themselves in that regard.”
Related stories
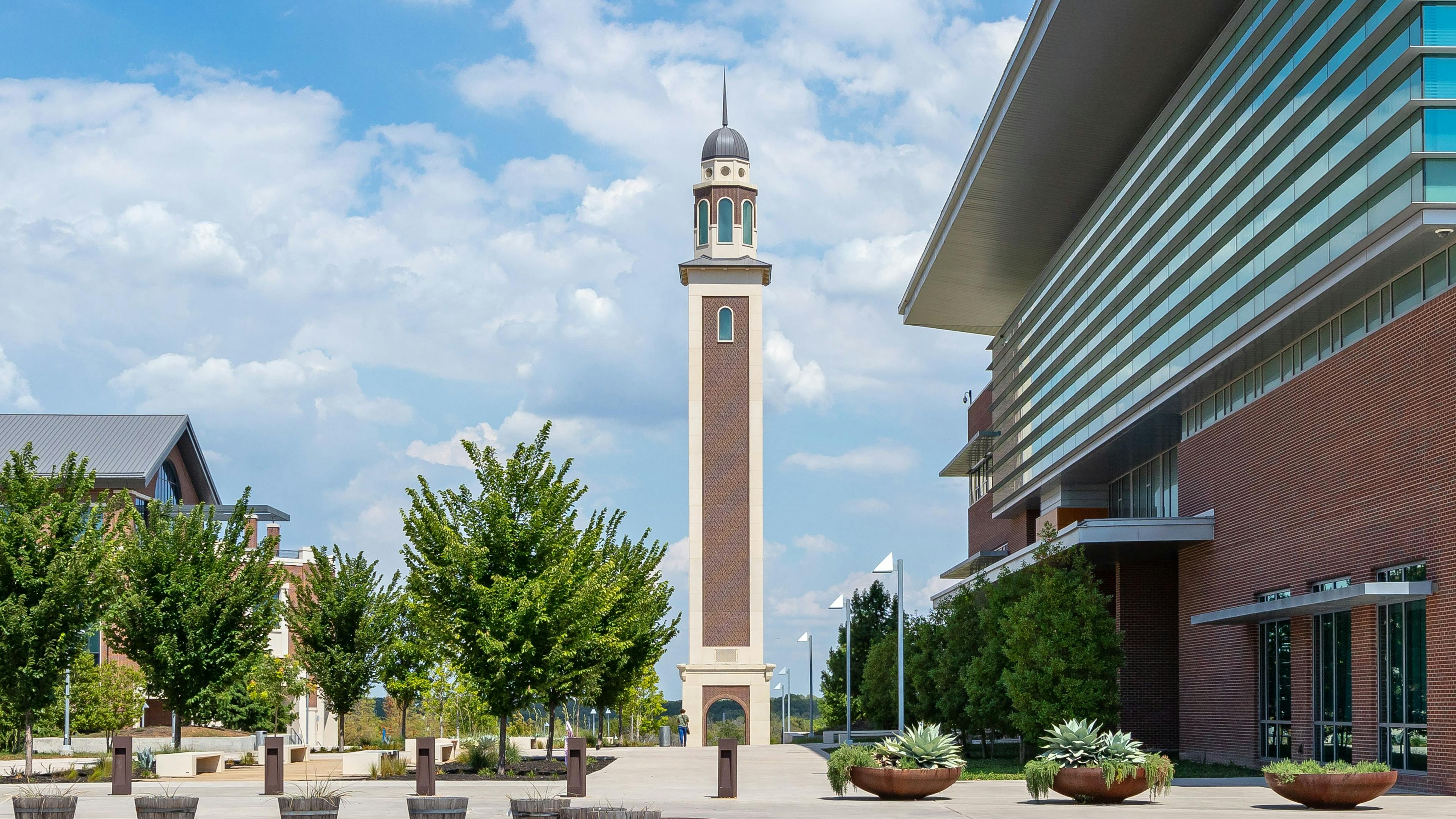
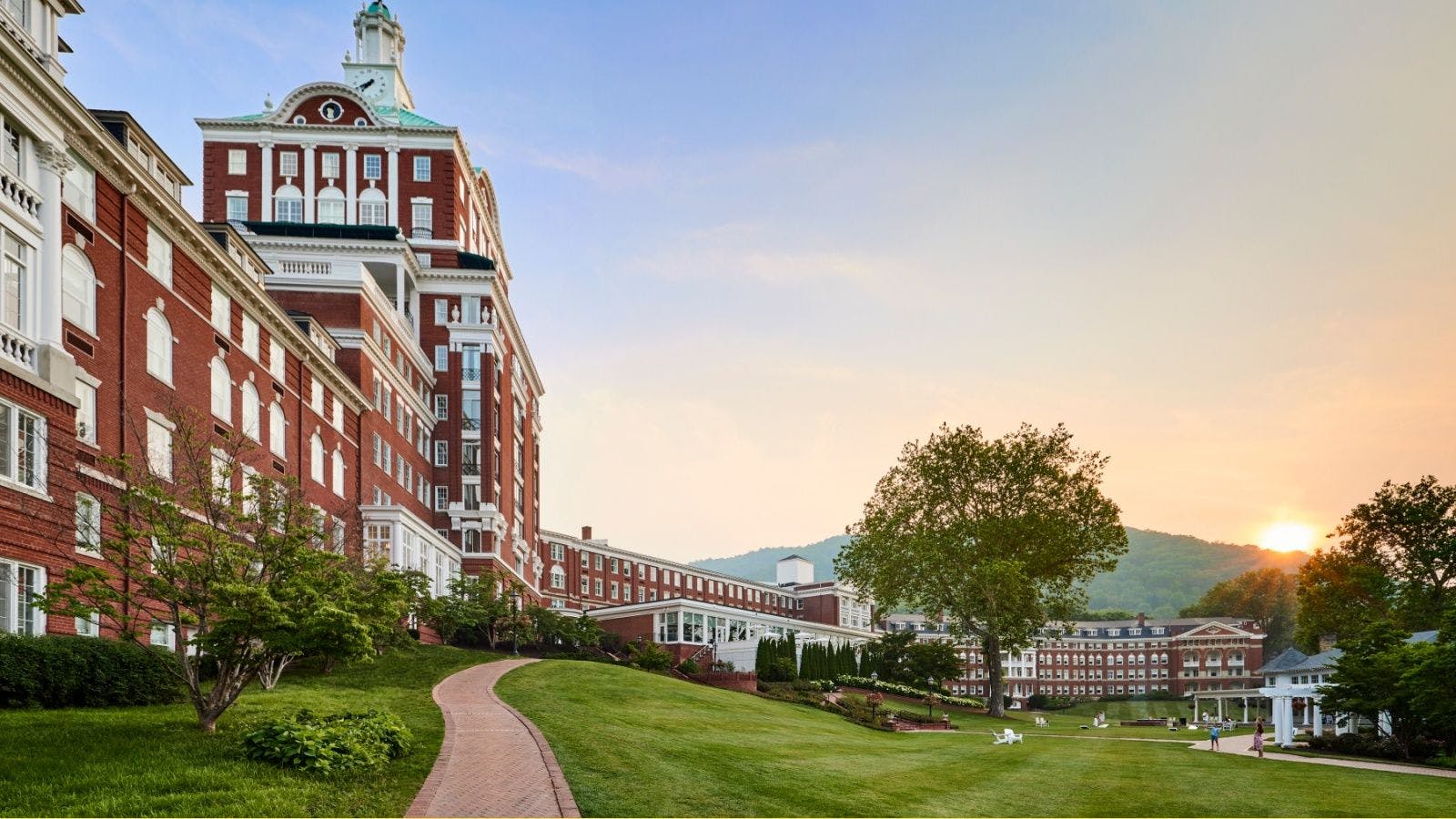
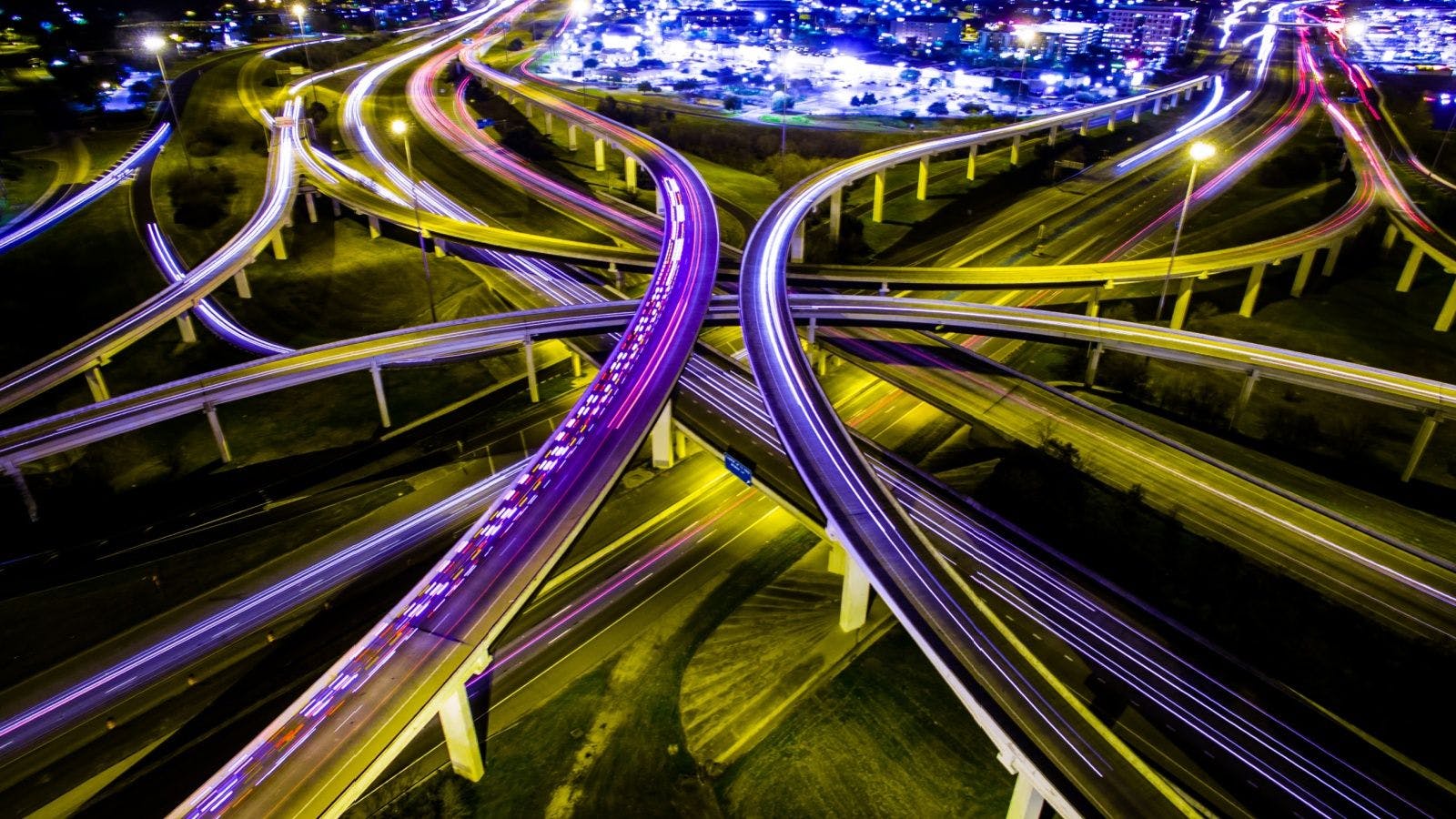