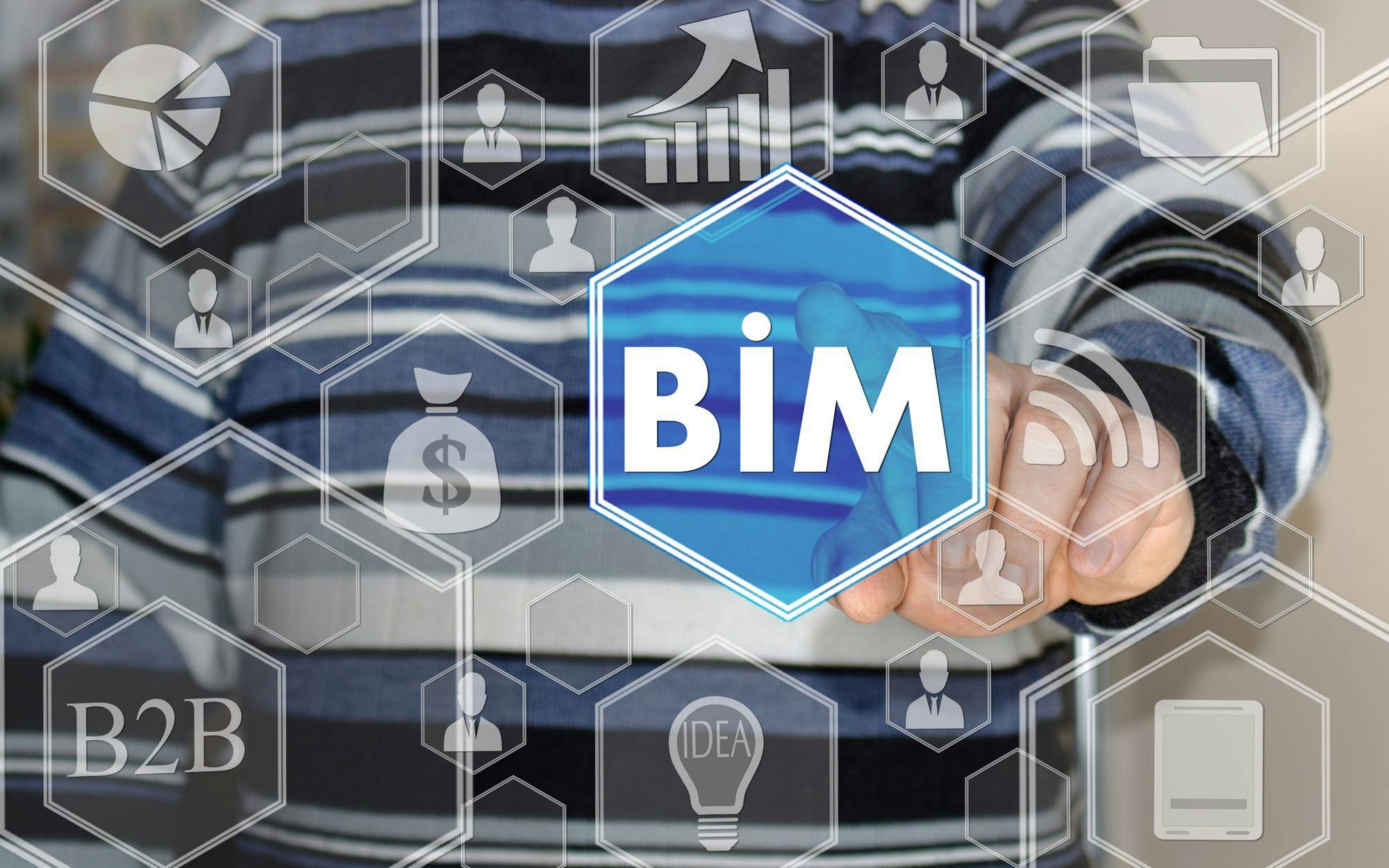
Glossary of Construction Industry Acronyms - Part I: AI Through GMP
The construction industry continues to experience a fast rate of change, having to adopt new technologies, different project delivery methods, emerging management techniques and more. Many of these changes seem to come with new acronyms…and that can lead to acronym overload.
In theory, a quick Google search would clear up any confusion. However, construction isn't the only industry that's become fond of acronyms, so finding a definition that doesn't pertain to an entirely different vertical can sometimes be challenging.
To help owners and other team members tasked with the construction of manufacturing and process facilities, here's a glossary of the most common acronyms used during project planning and development.
AI: Artificial Intelligence
AI applications use computer algorithms that improve automatically—or "learn"—through experience. They consist of a range of items that support basic functions in business, including machine learning, deep learning and computer vision. AI will continue to gain traction in the construction industry, especially in design, safety, testing, estimating, robotics and equipment/machine operation. Investments in AI are already paying dividends for contractors in the form of improved efficiency, safety and quality.
BI: Business Intelligence
BI consists of transforming raw data into meaningful information that can be used for business purposes and decision-making. According to Gartner Group, “BI is an umbrella term that includes the applications, infrastructure and tools, and best practices that enable access to and analysis of information to improve and optimize decisions and performance.” For construction firms, BI provides information across multiple systems and allows each person to succeed in his or her role. As part of BI, many construction firms are tracking key performance indicators (KPIs) on a company and project level. Ultimately, BI helps provide a clearer picture of what is going on in an organization or on a project.
BIM: Building Information Modeling
BIM involves creating and managing 3-D digital representations of a building and its systems—both the physical and functional aspects. BIM models support project design, visualization, estimating, scheduling and energy simulations, thereby providing clarity for the entire project team throughout the delivery process. A key benefit of BIM is that it allows project stakeholders to communicate and collaborate before construction even starts. Furthermore, BIM files can be modified and shared in order to manage and operate a facility over its lifecycle. BIM has become an essential tool in achieving project and business goals. Contractors have embraced BIM and have taken the technology to the field to improve construction operations.
CM: Construction Manager
CMs work on behalf of the owner by overseeing the construction process from preconstruction through completion. They act as the primary manager on the jobsite.
CRM: Customer Relationship Management
CRM describes a set of software tools that track a variety of information and data related to companies, individuals and opportunities. CRM systems in the construction industry have evolved to include project and individual histories, proposal history and marketing automation.
DB: Design-Build
With the DB method of project delivery, a single entity (the design-build team) works under one contract with the project owner to provide design and construction services. The DB model offers a single point of responsibility and is used to minimize risks for the project owner and to reduce the delivery schedule by overlapping the project's design and construction phases. DB integrates the roles of designer and constructor, with processes typically being led by the contractor. Having all stakeholders work in alliance fosters collaboration, efficiency and teamwork.
DBB: Design-Bid-Build
DBB is a project delivery method in which the agency or owner contracts with separate entities for the design and construction of a project. This is one of the most common project delivery methods used in the industry. The owner typically starts by retaining an architect or engineer to program and develop a scope of work, then to create the project plans, specifications and bid documents. The selection process for the architect can be competitive on a lump sum basis or it can follow a more traditional approach, in which the architect's costs are a defined percentage of the total installed cost (TIC). Once the detailed design effort has been completed, general contractors (GCs) are invited to submit lump sum or cost reimbursable project construction bids. The DBB method often results in wide bid spreads, requiring the owner to match project scope to bid scope. If the bids are within budget, a GC is selected based on a variety of factors defined by the owner and design team. Once the GC is selected, the GC begins to hire subcontractors for the various trades and the facility is constructed in accordance with the contract and construction documents, overseen by the owner and architect. Validation is then performed by a third-party consultant under the owner's direction. The competitive nature of the DBB process usually results in a competitive cost for the owner, but the quality of the subcontractors is left to the GC. Under this method, all construction and performance risks are assumed by the contractor. Scope variations resulting in change orders and schedule delays can occur if the owner's intent for the scope of work is not well-communicated by the architect to the contractor. While performance risks are assumed by the contractor, design and scope definition risks are assumed by the owner.
DBOM: Design-Build-Operate-Maintain
A DBOM contract assigns a single contractor the responsibility of not only designing and building a facility, but also operating it for a specified period of time. The DBOM method combines responsibilities for functions that are typically separated. This approach enhances project flow and provides the clarity that comes from partnering with a single provider. Typically, a long-term maintenance plan as well as estimates of associated costs are developed upfront.
ECI: Early Contractor Involvement
Similar to DB, ECI seeks to capture specialized knowledge on the part of the contractor during very early preconstruction. It involves a two-stage contract. Early contractor involvement offers advantages related to constructability, more realistic budgets and schedules, better pulse of the market, identification of long lead-time purchases that need to be made, and improved project delivery.
EMR: Experience Modifier Rate
EMR, also knows as mod rate, is a numerical value that represents a company’s annual losses in workers’ compensation claims. It is used to gauge a company’s safety performance and assess the future chance of risk. The lower the EMR of a business, the lower its workers' compensation insurance premiums will be.
EPC: Engineer-Procure-Construct
An EPC contract gives owners a single point of contact for their project. EPC firms handle design, procurement of all equipment and construction materials, and construction services for turnkey delivery of a facility, usually at a lump-sum price or cost reimbursable. EPC firms work with owners to develop a master plan at the onset of a project and incorporate that plan into the project estimate, schedule, budget and quality control. The firm has complete responsibility for the project from start to finish. EPC project delivery offers the tightest integration of activities during the construction process through a structured and disciplined approach. The EPC model reduces project risks for the owner, delivers predictable results and maximizes the effectiveness of capital planning. Engineering, Procurement and Construction Management (EPCM) is a special form of EPC contracting arrangement. Under an EPCM contract, the client selects a contractor that provides management services for the whole project on behalf of the client.
EVM: Earned Value Management / EVPM: Earned Value Project/performance Management
EVM is a project management technique that measures project performance and progress in an objective manner. The key factors in EVM are scope, cost and time. EVM can provide accurate forecasts of project performance and predict problems. Research has shown EVM principles are positive predictors of project success.
GMP: Guaranteed Maximum Price
A GMP contract is a cost-type contract where the contractor is compensated for actual project costs incurred plus a fixed fee subject to a ceiling price. Under this contract, the contractor is responsible for any cost overruns, unless the GMP has been increased via formal change order. Typically, savings resulting from cost under-runs are returned to the owner or are shared between the owner and contractor. GMP contracts are also known as GMAX, open-book contracts, not-to-exceed price, NTE or NTX.
Part 2 of the Glossary of Construction Industry Acronyms will continue with IoT through WELL.
Related stories
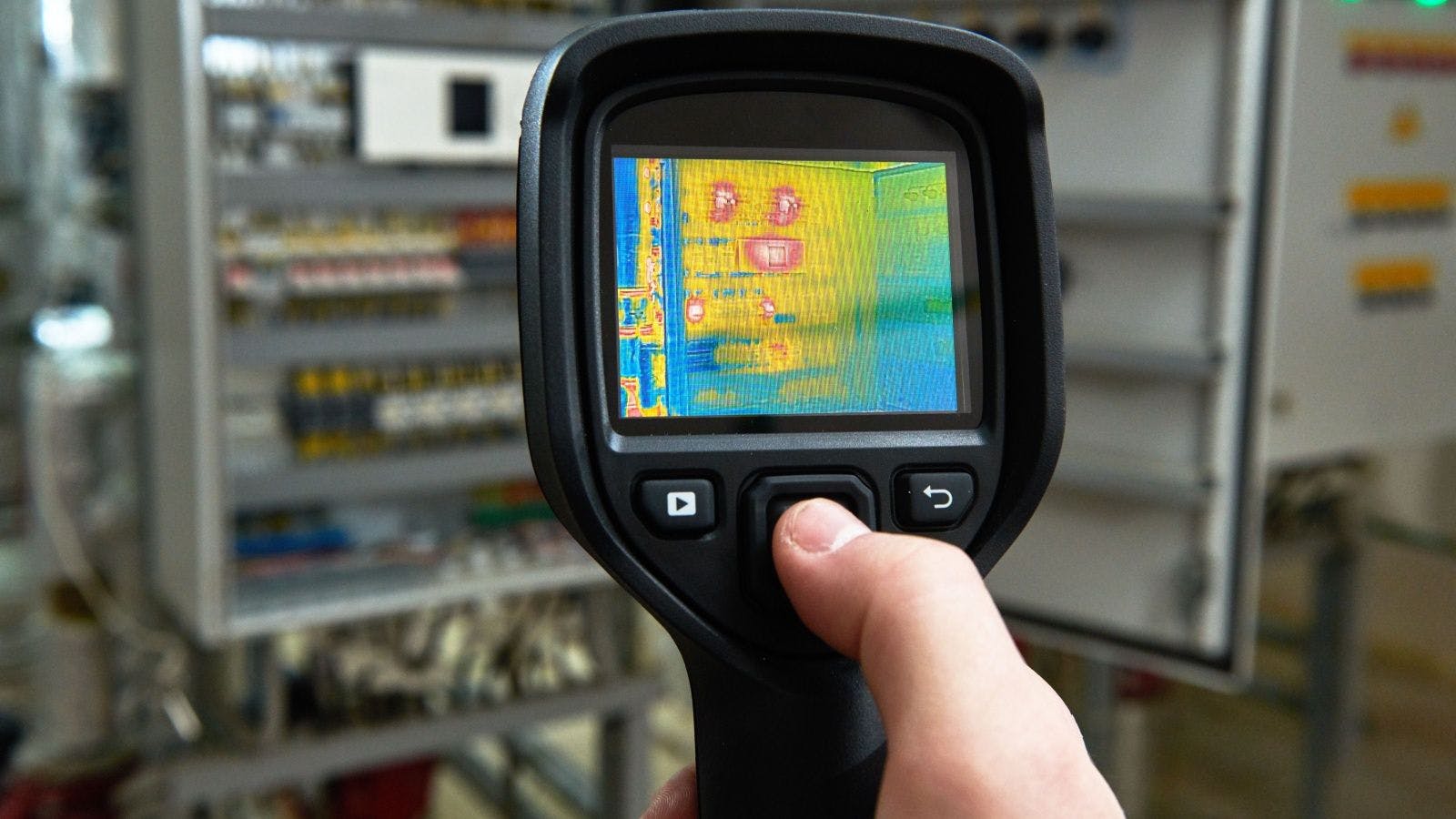
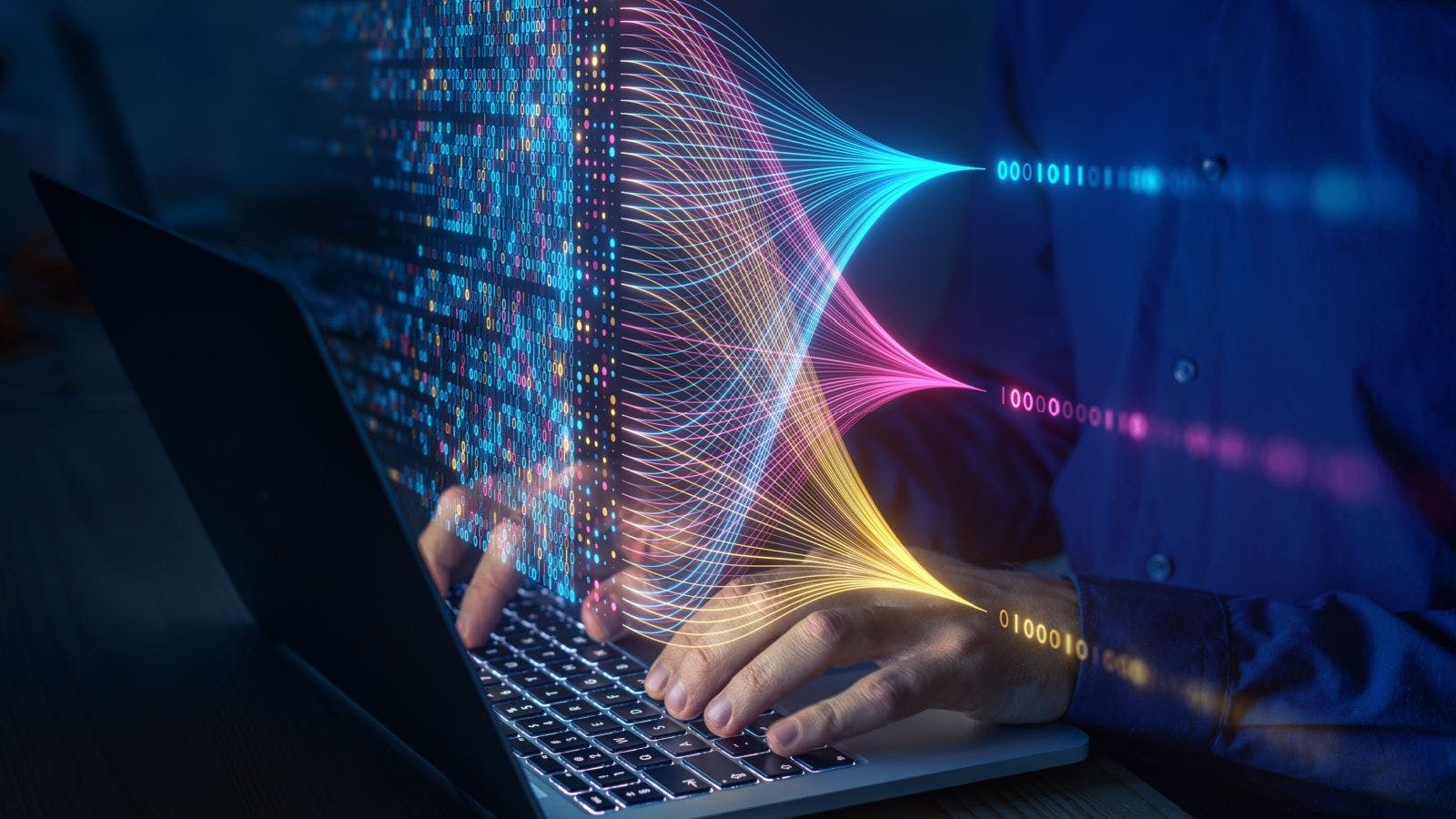
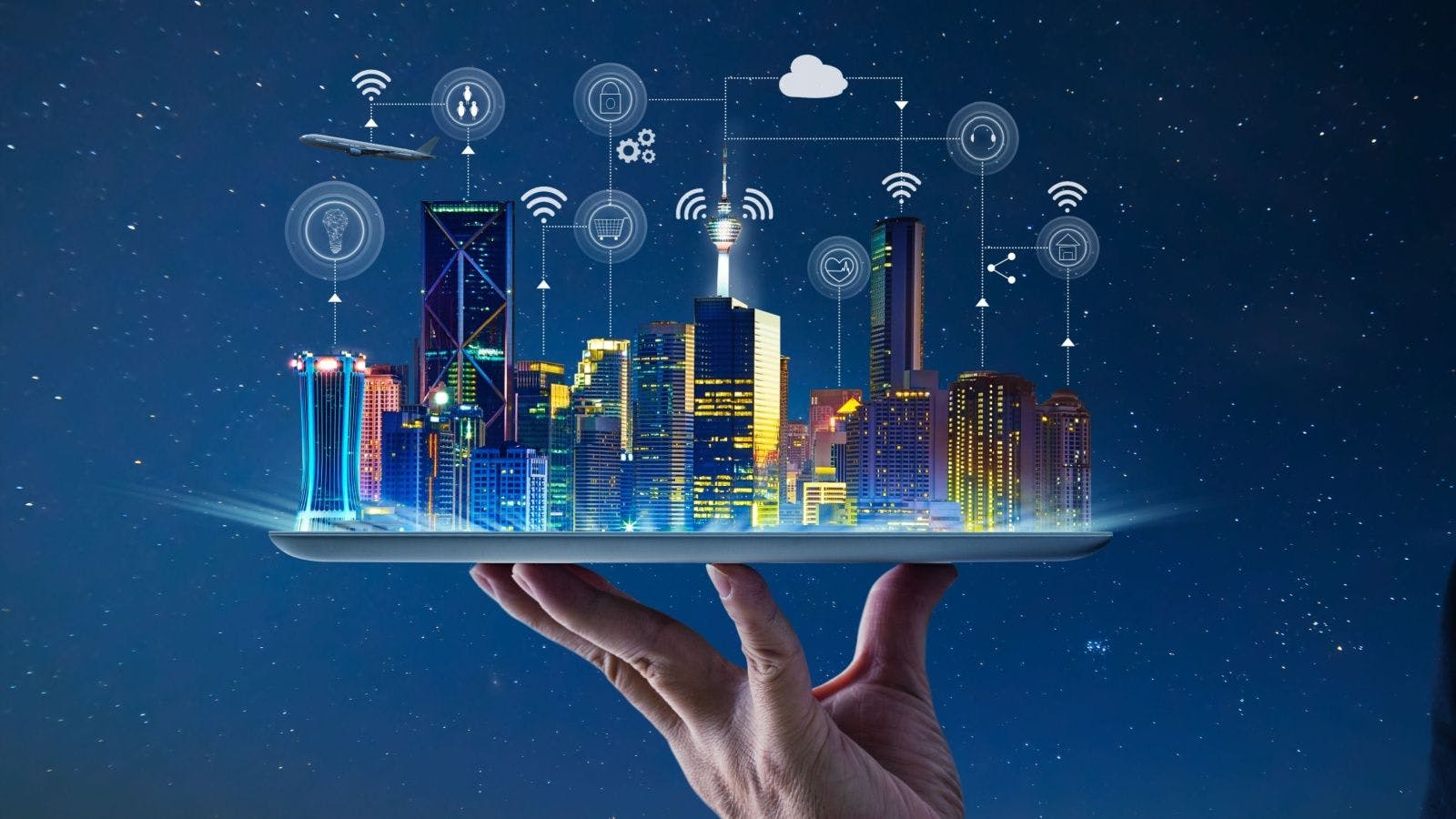